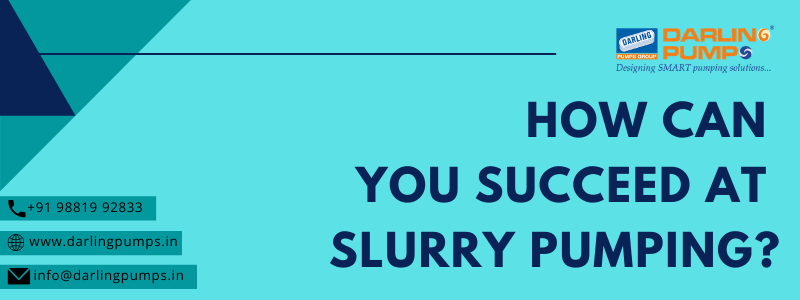
Everyone has been saying that the world has been paused due to COVID-19. But is it the case? What has really stopped? Probably you are still facing the same pumping challenges with your slurry pumps, if not more. During this lockdown one big change which is quite evident is that it has become more difficult for you to seek slurry pumping services.
As slurry pumping is a critical process it is always better to bank on experts. Well, be assured that you’ve landed in the right place. In this blog, we’re going to make you revisit points that will help you ease your slurry pumping process.
Firstly, it is imperative that in order to run successful slurry pumping you need to select the right pump for the same.
When we talk about plants, often they must handle slurries applications that range from processing to wastewater treatment. To deal with such mixtures is challenging, especially when you’re lacking guidance, like in times of quarantine. What is important over here is to check whether we have taken into account few critical elements like – Nature of slurry – abrasive / nonabrasive, Solid to water ratio, nature & size of solids & finally check if the nature of liquid is corrosive.
Frequently, the sites rely on centrifugal slurry pumps to pump out their slurries. Often been unaware about the limitations of these pumps in terms of wear resistant properties, solid passages as well as other adverse effects like settling of the solids.
Now, let’s look at some information that might help you go a long way with slurry pumping–
When it comes to horizontal centrifugal pumps, which are usually used for slurry services, many aspects need to be tailored to suit specific slurries which include use of liners, choice of materials and could even include different driver sizing.
• For slurry pump services, a pump operating at the best efficiency point (BEP) or on the left of the pump performance curve is usually preferred. As an indication, the rated point must lie somewhere between 85% to 110% of the BEP point.
• Major factors influencing wear are the following:
a) detailed information of erosive particles (size, material, shape, etc.)
b) solids’ concentration
c) particle and fluid velocity
d) hydrodynamic properties of the flow
In order to cope up with the wear, pump designers tend to generally rely on the use of thicker components or liners.
Now, let’s look at some questions that you should ask yourself before making the selection of your slurry pump–
• What pump style is suitable for your purpose?
• If you’re going for centrifugal, then is the material and the design of the impeller appropriate?
• What is it that the pump is constructed of?
• Keeping abrasive slurry in mind, are the discharge configurations appropriate?
• How safe is the given sealing arrangement for the application?
For more help with slurry pumping you need to bank on experts as there are still many questions you may have that are unanswered. Tough times demands reliable solutions. Be it virtually or personally, Darling Pumps is always a call away to help you.
Seek our virtual assistance at www.darlingpumps.in or contact +91 99819 92833.