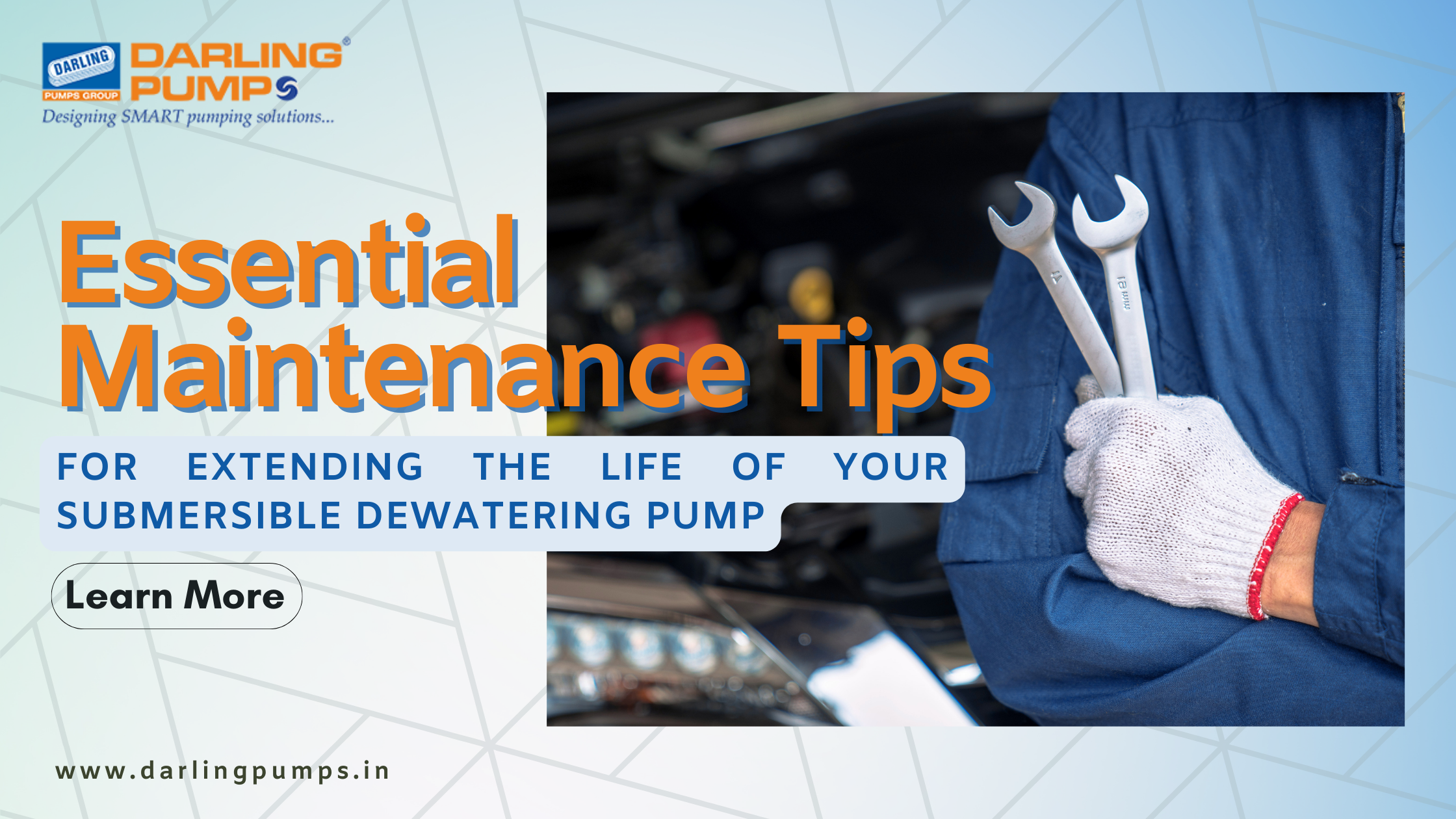
When it comes to water solutions, submersible pumps are some of the most valuable and versatile pumps for construction and mining, as well as residential and industrial needs.
However, to boost the efficiency of these pumps and ensure they last as long as possible, you need to maintain them. Regular maintenance is a critical element to help prevent unplanned downtime, to allow the realization of a low probability of repairs, and thus to make improvements in the pumps. Check out these useful guidelines to ensure that your submersible pump will perform to its maximum in the coming years.
1. Regular Inspection
To support the submersible pump maintenance, the essential time for the drainage pipe inspections is the critical point, which must be performed consistently. That’s why this proactive strategy is useful for identifying any small problem before it becomes a major one. While inspecting the pump, look out for signs of fatigue like squealing, rocking, or leaking around the pump. The presence of any debris or sediment around the pump’s intake should also be checked, because these will hinder the flow of water and overwork the motor of the pump.
This means that if you adopt the inspection schedule, you will stand a better chance of identifying these problems early enough and hence guaranteeing the best performance of your submersible pumps.
2. Check electrical connections
A submersible pump is greatly dependent on electrical connections to work optimally. Blown fuses, faulty control panels, improper or loose connections, or burnt-up wires lead to interference and, in some cases, the permanent demise of the motor. It is important to check periodically all existing electrical connections to see whether they are tight, proof against dampness, and whether they show signs of corrosion.
When performing the cross-checks, make sure that the grounding of the pump is alright because good grounding will help avoid electrical problems, safeguard the motor against surges, and make it safer for people who are operating it.
3. Monitor operating temperature—overloading
High temperatures due to overloading pose a significant risk to the lifespan of the submersible pump. If for a long time a pump performs the function of pumping, for instance, if it does not take adequate breaks or if it experiences high loads, it tends to overheat. Many pumps work only in a particular range of temperature, and if the temperature rises beyond this range, the motor is affected or may fail.
To prevent overheating, you have to pay much attention to the operating temperature of your pump. For some pumps that need to operate continually, then the user should change the operating time and loading sequence, or if the pump is dipping in the knee or shallow water, then the user should incorporate cooling systems on the pump. That means when you are keeping the temperature at the right level, you are shielding the motor as well as enhancing efficiency.
4. Keep the pump clean
Silt, dirt, and other materials can build up around a submersible pump, especially in complicated settings such as construction tasks or settings where the water contains minerals. These particles can be sucked by the pump intake and block the suction, decrease water circulation, and overload the motor. A clean pump performs better but also takes less damage from blockage and heavy grime compared to a dirty one. Also, in the case of storing the pump for a considerable time, the pump should be flushed out by clear water.
5. Limit the vibration and noise produced
Such sounds or vibrations are usually initial signs of problems with a submersible pump. A loud sound from a pump or frequent vibrations next to the pump could be a consequence of conflicting adjusted screws or bolts, misaligned parts, or worn-out parts.
Any forms of vibration should be checked, and the pump should be stopped until it is confirmed that there are no loose or misaligned parts. Continual vibrations, if unresolved, could result in further destruction and hence a cutoff of the desired efficiency in the pump. Regular inspection of your pump will also help you detect the root of the problem early and avoid spending a lot of money on its repair since a faulty pump will cause a lot of issues that will need repairing.
6. Ensure Proper Placement
The place where a submersible pump is installed greatly determines its lifespan. Locating the pump where the water depth is low or densely covered with debris puts pressure on the motor as well as the possibility of clogging. Secondly, submersible pumps require a minimum submergence level to pump out effectively and thus should be installed in water that is deep enough (up to its minimum submergence level) to avoid heating up.
7. Look at the Impeller
The impeller is used to facilitate the circulation of water, and any flaw in the impeller will to some extent affect the performance of the pump. In particular, if the pump operates with heavy sediment or abrasive materials, the impeller should be examined for wear, corrosion, or clogging regularly.
8. Observe the power consumption
Any increase in the amount of power being used without a corresponding increase in the amount of solid concentration in the pumping liquid. A faulty pump means more energy consumption per process, high chances of overheating, and consequently motor burnout.
Observing the power demand of the pump gives very useful information regarding the status of the pump. If power consumption becomes high, then it is high time to look out for blockages, clogged impellers, or electrical complications. Daily monitoring gives you an opportunity to identify areas of inefficiency early and correct them in a way to minimize the stress on the pump.
9. Use the Manufacturer’s Schedule for Maintenance
Each manufacturer supplies its guidelines on how to maintain its submersible pumps for their specific models. This is a list of advisories on the timeframes within which the machine should be inspected, components replaced, and operating advice. It is possible to observe important differences in the pump operation and its life cycle depending on compliance with these suggestions.
Respect the manufacturer’s recommendations when it comes to parts replacement, particularly seals, bearings, and impellers. Failure to heed these guidelines is likely to result in some uploads developing faults and calling for repairs, which are usually costly.
Conclusion
Following maintenance practices and requiring submersible pump manufacturers’ guides will help to enhance the performance and durability of your submersible pump. Doing this is helpful because it will be monitoring for a condition that needs repair, thus helping in reducing the cost of repair, and it will also be maintaining the cleanliness of the pump, thus increasing its life, and maintaining all the conditions provided by the manufacturer.
If one wants to get submersible pumps, the best pump manufacturer in Indore, Darling Pumps, provides quality and efficient submersible pumps depending on different needs. Such pumps are often referred to as workhorses because these come with the best reputation of being reliable and great-performing pumps, which means you get a pump that is built to endure. A properly maintained submersible pump is one of the most valuable tools in any operation today because it guarantees a long-lasting service to the desire of the owner. Contact Darling Pumps today for all your pumping needs.